Description
Conceptualization, design and fabrication of a personal companion lamp.
Gated product development process with iterative improvements in design and manufacturability.
Fabrication of multiple units based on standardized processes emulating mass manufacturing.
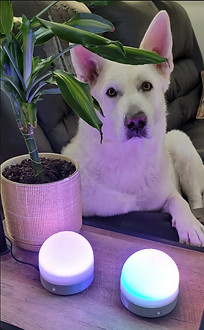
Lumi Light
Contributions
-
Product definition and design
-
CAD models and drawings
-
Product Specifications documentation and testing
-
Resin casting and silicone molding
-
3D printing
Identification
This project was focused at observing the product development process, gated project management and design for manufacturability.
The assignment constraints pushed for:
-
Creating a simple electromechanical product with 5-10 BoM components
-
Usefulness in day-to-day life
-
Utilizing different manufacturing processes
-
Overall marketable product cost < $20
Ideation
The idea of creating a lamp instantly clicked for our team. It fit the bill for most of the criteria of the project, and would help us carry out something useful and lovable at the end of the assignment.
Several concepts were created based on form-factor and actuation mechanism for the lamp. Based on priorities, the team gravitated to the following features:
-
Easy to switch on-off: The lamp was supposed to be operated in low light or pitch black darkness
-
Configurable lighting: Mood setting and ambience
-
Soft, amicable form-factor: For an intimate setting and use
-
Glow in the Dark: A useful feature for locating the lamp when used in darkness
-
Small and easy to hold/ carry: The lamp would be designed to be a companion article
-
Rechargeable: An inbuilt battery would enable several more use-cases than an active cable




Concept Sketches

Initial Assembly
(Helped plan for and target development)
Prototyping and EVT
The product idea with a soft top and easy to actuate design was adopted. What followed was design and development in the following aspects:
-
Actuation mechanism: Tested mic based switch, vibration sensors
-
Form-factor and sizing
-
Mold-making and silicone top creation

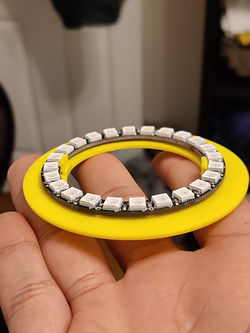

EVT Prototype
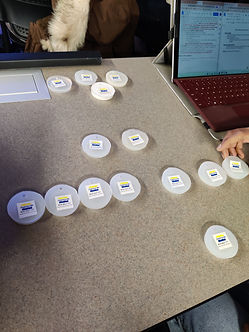
Sampling Silicone Grades for Soft Top

EVT electrical Layout
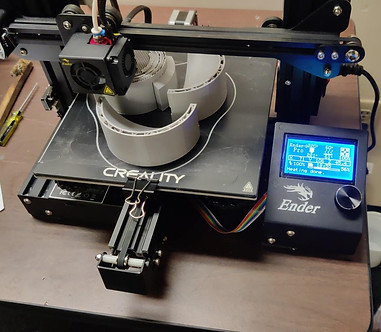
Mold Printing for Soft Top
Mold Design Evolution

V1
-
EVT Prototype Test
-
2 Part Mold with core
-
Locating features for assembly during cure

V2
-
Improved surface finish with SLA print
-
Changed soft top design to interference fit
-
Improved locating features for stability in part thickness

Final Mold
-
Integrated pouring spouts for cleaner part seam
-
Surface finished to desired grit
-
Finalized part dimensions and interference
Final Design

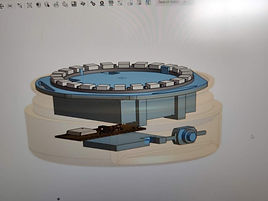

Final CAD
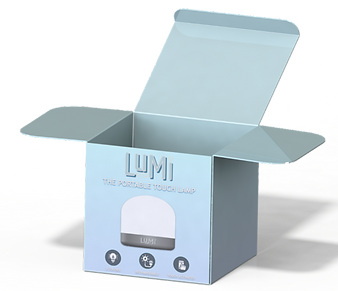

Packaging Design and Render
Lessons Learnt
-
Moving with high risk items first: we struggled with defining the best actuating mechanism and continued to optimize for and iterate with different vibration sensors and mics which had design implications
-
Failing fast: Early iterative investigation of silicone soft top molding among drip molding, coreless molding and inside-out molding were helpful in identifying quality and performance risks
-
Graveyard of failed attempts: As an engineer it is important to address the existence of failed methods and prototypes.
-
Significance of standardization of process
Gallery
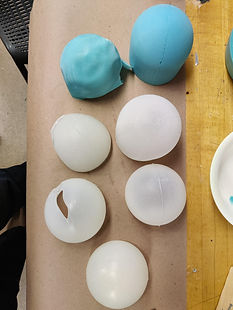


Failed Prototypes


Design Evolution


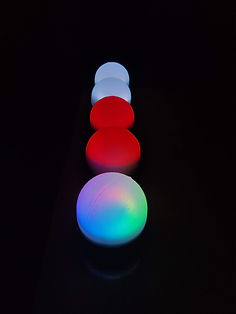
Final Built Units

Glow in the Dark Top
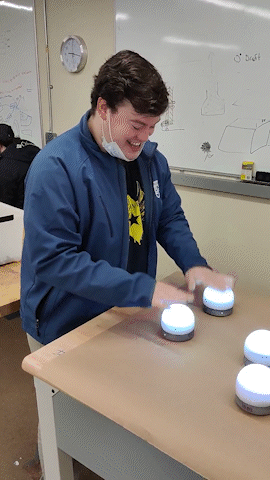
Tap and Shake Activation

Final Presentation